Mini Cleanroom for the Manufacture of Advanced Therapy Medicinal Products (ATMP): Bioengineered Corneal Epithelium
Keywords:
Advanced therapy medicinal products
Ophthalmology
Hospital pharmacy
Citation:
Berisa-Prado, S.; Vázquez, N.; Chacón, M.; Persinal-Medina, M.; Alonso-Alonso, S.; Baamonde, B.; Alfonso, J.F.; Fernández-VegaCueto, L.; Merayo-Lloves, J.; Meana, Á. Mini Cleanroom for the Manufacture of Advanced Therapy Medicinal Products (ATMP): Bioengineered Corneal Epithelium. Pharmaceutics 2021, 13, 1282. https://doi.org/10.3390/ pharmaceutics13081282
Statistics and impact
0 citas en

0 citas en
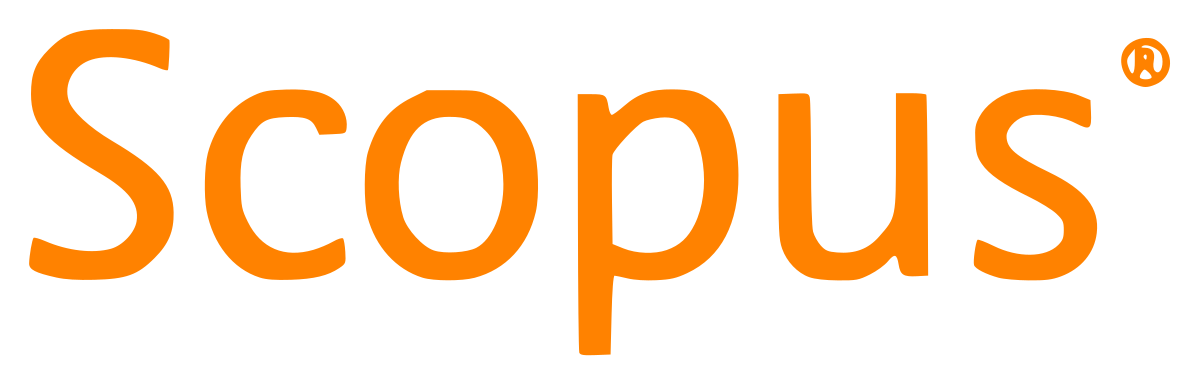
Items in Dadun are protected by copyright, with all rights reserved, unless otherwise indicated.